In an interview with Brian of Reifsnyder Precision Works we get a history on the development of Genuine J-Head™ and on the decision to use PEEK a truly space age plastic!
The story behind the PEEK.....
Get your teddy bear, blanket, and have a seat.
Ok. Once upon a time....
Well, originally only PTFE was used because it is slippery and a really good insulator. The idea was the PTFE would hold the brass heater barrel and nozzle (they were separate parts)
The PTFE is horrible at supporting something. So, PEEK was tried and it worked great for ABS but not PLA.
So, somebody suggested a sleeved arrangement where the PEEK was a support structure.
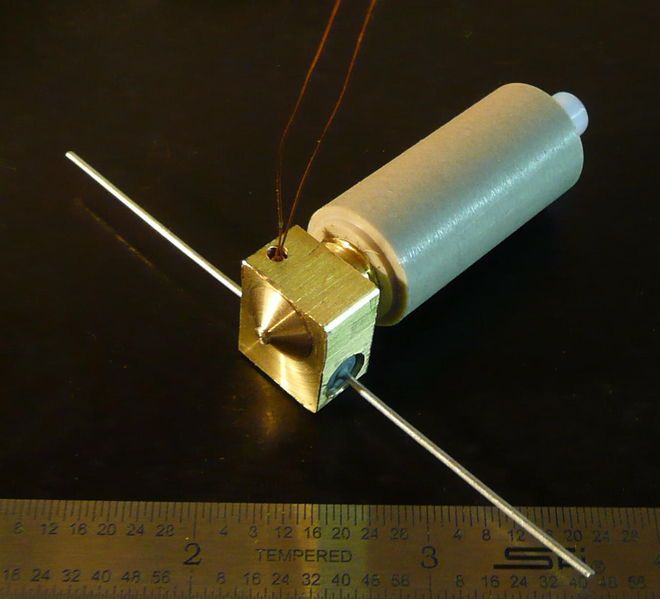
MK1 J-Head - the first
So, sleeved hotends were born. This lasted for a while but the hotends were still miserable.
Eventually, the J-Head was conceived as an easier to use hot-end.
The tan one, in the picture, was the first production J-Head.
There is no cooling zone as only ABS was used at the time. PLA still wasn't used much.
You can see the ptfe liner sticking out of the top.
The idea was to keep it simple and have the extruder hold the ptfe in place. But, this was a problem and didn't last long.
Other hot-ends (i.e. makergear) used a ptfe liner that was pinned in place. But, I wanted something simpler and knew about hollow set screws. So, I found a size that was perfect and used that to retain the liner
The second J-Head is the Mk II.
But, PLA was a major PITA to print with these because PEEK and PTFE are both insulators so the heat was kept in the core.
The Mk III has that aluminum heat sink.
Really neat arrangement.
The heat sink has a 1/4" hole through it for the PTFE liner to pass.
The heat sink was a pain to machine with the tools I have, though. Also, the liner hole had to be pretty precise and the hole in the PEEK had to be really precise.
I also made a tool to properly align that heat sink when it was installed as it was very difficult to properly align otherwise. If it wasn't properly aligned, the liner would not pass though it.
I got to thinking about this problem and wondered if it was possible to keep the heat from building up another way.
Since the PEEK is an insulator.....why not simply remove the PEEK?
So, I machined out a vent on a piece of PEEK to see if there was enough space to do so.
I guessed that if there was 1mm or about 0.040" of PEEK between the liner and the air that it should provide enough material to support the liner while removing most of the insulation around the core.
The struts are to provide the support for the hot-end.
Removing the insulation works almost as well as having a heat sink and it was a success.
So, that became the Mk IV.
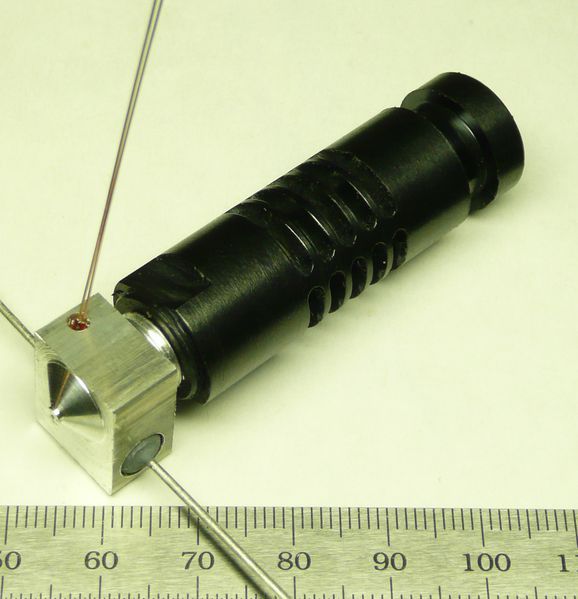
MK4 J-Head - the fourth
There was a couple variations of the MK IV, though. Through feedback, it became obvious that the melt chamber needed to be much better.
The original concept was that you could simply change out ptfe liners to configure a hot-end for 3mm or 1.75mm. But, that left a very, very short melt chamber.
So, I made two brass nozzles. One for 3mm and one for 1.75mm with the only difference being the size of the melt chamber.
People were liking J-Heads but said they were too long.
I wanted to see if using 1/2" x 1/2" brass was practical so as to have a smaller heater block to heat as well.
So, after a lot of experimentation with what I called the mini J-Head, I came up with the Mk V
I kept the same length of cooling zone within the PEEK while lengthening the melt chamber to the entire length of the brass.
So, by using the entire length of the brass, the PEEK also became an insulator for the upper section of the melt zone.
With the Mk V and newer hot-ends, the PEEK now does the following
- Provides a place to mount the hot-end.
- Retains the PTFE liner and ensures that it doesn't deform.
- Has a cooling zone to keep the core cool for as long as possible.
- Holds the brass melt chamber/heater block/nozzle.
- Insulates the upper part of the brass melt chamber. (The threaded part)
So, that is the story of the PEEK. There is really more to the story. But, that is why PEEK.
I like the PEEK because it is one part that performs many functions very well.
When compared to an all-metal hot-end, the PEEK replaces two parts. The heat sink and the stainless steel "heat break".
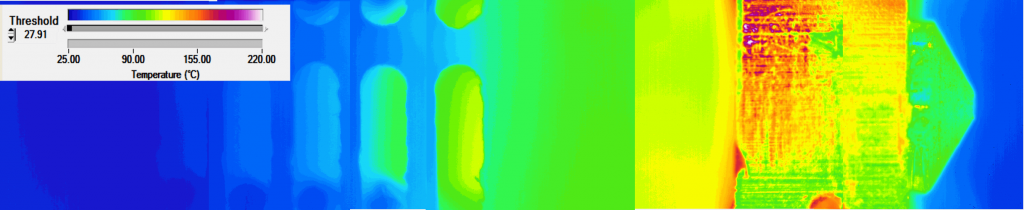